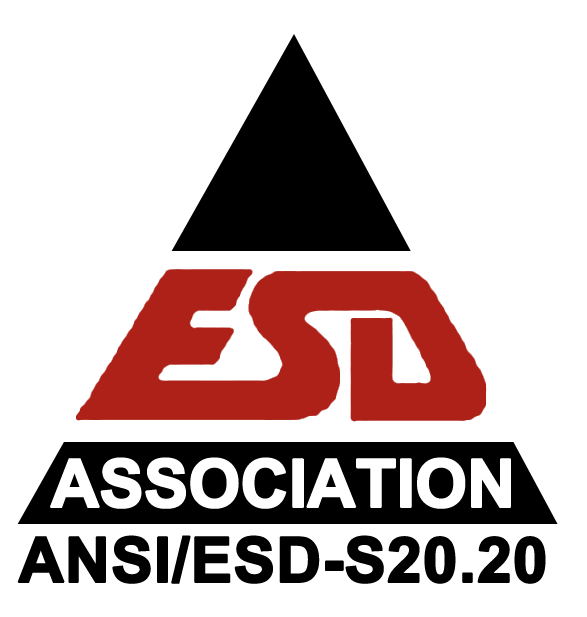
Static electricity, also known as electrostatic discharge (ESD), is an electrical charge at rest, it builds and looks for somewhere to go. The discharge can cause three types of damage: catastrophic, latent and upset failure.
Lightning is probably the most recognizable effect of static electricity. Generating millions and millions of volts, and we all know the damage lightning can do to property and people.
Another recognizable effect of static electricity is the shock you receive when you slid out of a car in dry weather conditions and feel a zap. The human body feels a shock when the voltage is higher than about 3,500 volts. Walking over a carpet can generate 35,000 volts. The Electrostatic Discharge (ESD) from this voltage can cause pain. The discharge is not life threatening but it still hurts!
In simple words, static electricity is the imbalance of charges. The main electronic component affected by these devious charges are semiconductors. Static electricity causes damage to sensitive electronic components, so if one brings it near electronics, there will be failure.
The static electricity that concerns the electronics industry is the discharge that you cannot feel or see. Static electricity at low voltage levels is real even though you cannot feel or see it. Integrated circuits (IC’s) have different levels of ESD sensitivity. Electrostatic voltages can be generated by the things we do all the time such as brushing your hair or rubbing your clothes together.
Today, most companies recognize the value of a complete static control program. Implementing a static control program may cost a few dollars in the beginning but in the long term can save money, boost reliability of product, and enhance a company’s reputation in the field.
A catastrophic failure of an electronic component can be the least costly type of ESD damage as it may be detected and repaired at an early manufacturing stage. Latent and upset damage caused by ESD is potentially costlier since damage occurs that cannot be felt, seen or detected through normal inspection procedures. These defects can be very expensive as the product passes all inspection steps and the product is completed and shipped. The defects can severely impact the reputation of a company’s product causing intermittent failures after shipping a product that can be frustrating, particularly when the customer returns a product.
It is critical to be aware of the most sensitive items being handled in your factory. As electronic technology advances, electronic circuitry gets progressively smaller. As the size of components is reduced, so is the microscopic spacing of insulators and circuits within them, increasing their sensitivity to ESD. The need for proper ESD protection increases every day. A systematic static control program can add to your company’s bottom line.